「3D打印房屋的功能与事实」
打印房屋的技术正在慢慢发展,代码与供应商都可以找到解决方案,使得其最终成功。
译文:
Jennifer Castenson
3D打印让世界可以立马获得实物商品,而消费者们又总是渴望定制并且希望得到即时满足,因此,3D打印变得越来越流行。
在荷兰,第一座3D打印的桥已经可以步行甚至骑车通过。科学家们发明了3D打印的器官、假肢、定制的鞋、包装、产品开发模型甚至是火箭。就像住房一样,这个行业还没有应用3D打印,但一些先行者已经开始了尝试。
缓慢的开始
当第一个3D打印的家出现时,世界为之震惊,但是,这项令人惊叹的技术仍处于不够成熟的阶段。新闻标题里引起轰动的3D打印房屋并不足够精细成熟,缺乏必要的基础设施而不能满足人们的永久居住。
D-Rad的创始人马修·罗森伯格(Matthew Rosenberg)正在加州马里布(Malibu)与一名开发人员合作,试图解决该技术在住宅领域所面临的一些挑战。Rosenberg和他的团队正在开发一个完全集成的打印程序,可以提供完整的机械、电气、和管道组件。Rosenberg说,为了避免浪费,3d打印房屋的基础设施的选择要比一般的平面设计更加有限。目前,他的团队正致力于找到配置必要的管道的方式与合适的代码,以便可以支持打印过程。
这个名为“打印房子”(Print House)的项目,由创业公司传奇蒂姆•德雷珀(Tim Draper)和他的创业大学里2016年最佳毕业生托尼•卡帕索(Tony Capasso)支持,Tony拥有一家建筑自动化公司,该公司的目标是通过减少施工现场的停工时间,以消除施工过程中效率低下的问题。
“打印房子”的目标是通过3D打印技术进行混凝土分层,从而改变混凝土材料的制造方式,这个过程可以使得砌砖、拱式建筑以及蜘蛛网络似的轮廓灵活性三者得到最好的结合。目前,这个项目仍然在马里布的推进,不管结果怎么样,最终都将是3D打印、创新设计、可持续性与施工过程的一个真实案例。
为了完成其他3D打印房子没能完成的事情,这个团队不得不考虑如何整合基础设施。他们是这样做的:通过使用钢筋和铁丝网来控制管道和电气等,而这个房子则是利用四种现场打印机来打印。Rosenberg说他们正在申请专利,因此不能透露实验项目中的细节。
雅各布·乔根森(Jacob Jorgensen)是另一家名为3D printhuset的3D打印公司的技术经理,该公司在阿姆斯特丹建造了一个完整的项目。在他的项目中,水、电和污水的部分都是由第三方公司在地基边缘打印后完成的,板基础也同样由第三方公司完成。
另一个在3D打印领域崭露头角的是2016年HIVE100获奖者Platt Boyd,Branch Technology的创始人和首席执行官。他的公司目前正专注于一个名为“曲线吸引力”(Curve Appeal)的项目,这个项目由WATG建筑公司设计,将会在12月开始打印。
一些合作伙伴正在与分支技术进行调整,以学习和体验该项目如何与所有基础设施元素(包括USG、Sub Zero和Philips)相适应,也为这个史无前例的项目提供产品,作为未来演示的一部分。分支技术将使用机器人在预制过程中进行3D打印面板;然后这些面板被带到工地,像乐高系统一样组装起来。打印过程比其他的项目要密集得多,具有双重墙壁的强度。
巨额节省
新的建造过程有着一系列的好处。房子将会在几天内建好,而不是几个月。考虑到劳动力成本和运营,这个极度的时间节省对于建造者来说无异于节省了花费,而这个节省最终也会传递到消费者,带来消费者的节省。
在Print House项目上,Rosenberg预测将可以减少90%的浪费,因为在建造过程中唯一额外需要的材料仅仅是他们用在打印过程中的支持性材料,也不再有利用框架性模板的必要。
在有关节省时间上,两个项目的开发者都难以预测3D打印将在多大程度上改变时间计划。Jorgensen猜测,毛坯房需要花费大概50个小时来打印完成,比传统方法快了很多。但是,由于这是第一次试验,存在一些比较耗时的打印机和设置的不断调试,而这在未来是不需要考虑的。
法规会如何改变?
随着不断发展,新的法规必然会产生。
“我们一直在不断的改进法规,
”Rosenberg说,“我们建立起了主干部分,知道何时对它进行合适的改变。对这个项目和其他项目,努力保持在法规前沿的位置,用我们认为正确的方向引导城市。比如,我们向卡尔弗城提交了一项有关分区法规和法律语言的议案。”
当Jorgensen刚刚成立3D printhuset时,他的团队并不关注改变原始法规,因为这太耗时间了。Jorgensen说,“相反地,我们根据法规来调整我们的建造,诸如在房子内部有支撑房顶、防风的柱子等。”
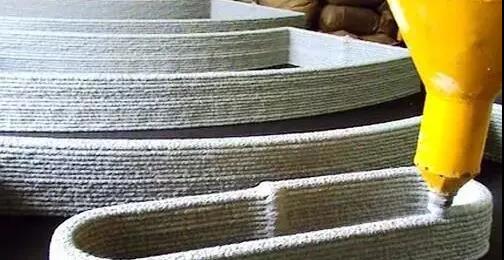
未来是什么样的?
首先,3D打印让新的形状和创意走进生活,这会使得设计发生变革。这个顺其自然的发展将融入越来越多的功能,比如在印刷过程中的绝缘、管道和电力,这都使得3D打印更加快捷和高效。“但是目前世界上还没有一个项目接近这个成熟阶段,我们也不知道到达那样的水平需要多长时间。”Jorgensen说。
Rosenberg和他的“Print House”团队想逐步采取行动,利用这项技术在第三世界国家建造房屋。他说,“我们首要解决洛杉矶在建筑方面的分散和效率低下问题。”“我们希望可以在一个地区内密集建设。”
他们面临的最大挑战
“让深入人心的经典建筑技术真正的成为过去是困难的,尽管这些技术效率低下而且过时了”,他说,“我们必须完成第一个项目,向人们显示出更少的人力使用并将其量化,来改变人们的固有观点,这一直都是最难的部分。”
Maura McCarthy,是Blu Homes公司和HIVE dean的联合创始人,将给她在HIVE的小组一个挑战,去想出新的方法提升建造过程效率,并突破传统的实践。
原文:
Function and Facts of3D Printed Housing
The technology for printing homes is slowly evolving so that code and suppliers can develop solutions to make it successful.
By Jennifer Castenson
3D printing gives the world instant access to goods. And because of consumers' desires for customization married with instant gratification, it is becoming more and more popular.
The first 3D-printed bridge has opened for foot and bicycle traffic in the Netherlands. Scientists have 3D printed internal organs, prosthetic legs, custom shoes, packaging, product development models, and even rockets. As housing does, the industry isn’t diving in to be the first adopter, but several innovators are dipping in their toes.
Starting Slow
The world was amazed to see the first 3D-printed home. And although the technology is amazing, it’s still relatively immature. The 3D-printed homes that made a big splash in the headlines are not yet sophisticated enough for someone to live in them permanently; they lack the necessary infrastructure.
Matthew Rosenberg, founder of M-Rad, is working with a developer in Malibu, Calif., to solve some of the challenges facing this advancing technology in the field of housing.
Rosenberg and his team set out to develop a fully integrated printing program that offered complete mechanical, electrical, and plumbing components. To avoid waste, the options for setting up the infrastructure for a 3D-printed home are much more limited than on a normal floor plan, said Rosenberg. His team is working on ways to configure the necessary pipes and conduits that fit code and that can be supported during the printing process.
The project, called Print House, is backed by startup legend Tim Draper and his Startup University’s 2016 Best in Class winner Tony Capasso, who owns Construction Automation Inc. It aims to rid the construction process of its inefficiencies by alleviating downtime on site.
Print House's goal is to change the way concrete materials are made by moving to a process of concrete layering in 3D printing. The process brings the best of bricklaying and arch-building together with the contour flexibility of spider webs. The project currently depends on permitting in Malibu to move forward, but will be a true example of 3D printing and innovation in design, sustainability, and the construction process.
To do what other 3D-printed homes haven’t been able to accomplish, the team had to look at ways to incorporate infrastructure. They are doing so by using rebar and wire mesh to hold plumbing and electric conduits in place while the home is being printed with four onsite printers. Rosenberg says their process is patent pending and couldn’t reveal the details during this experimental project.
Jacob Jorgensen is the technical manager of another cutting-edge 3D-printed home called the 3D printhuset, a completed project built in Amsterdam. For his project, the water, electricity, and sewage portions were done by a third-party company after the foundation rim was printed. The slab foundation was done by the third-party company as well.
Another up-and-coming player in the realm of 3D printing is 2016 HIVE 100 honoree Platt Boyd, founder and CEO of Branch Technology. His organization is currently working on a project called Curve Appeal that was designed by architecture firm WATG and will start printing in December.
Several partners are aligning with Branch Technology to learn and experience how the project fits together with all its infrastructure elements, including USG, Sub Zero, and Philips. These partners are contributing product as part of a future demonstration for this unprecedented project. Branch Technology will 3D-print panels in a prefabrication process using robots; the panels are then brought to the jobsite and put together like a Lego system. The printing process is much more intensive than other projects that Branch has done, with a double-walled strength.
Huge Savings
This new construction process promises a host of benefits. Homes will be completed in days, not months. This extreme time savings will equate to cost savings for builders, in terms of labor and operations. That savings can then be passed on to the buyers.
With the Print House project, Rosenberg predicts about a 90% reduction of waste, because the only extra material in the construction process is the support that they are using during the printing. There will no longer be the need to use formwork.
As for time savings, the developers of both projects have a hard time predicting a true number for how 3D printing could change schedules. Jorgensen guesses that the raw house, which takes approximately 50 hours to print, is faster than some conventional methods. But since it was an experimental first time, there were a few time-consuming adjustments to both the printer and the setup that would not be future considerations.
How Will Code Change?
With new processes, new code will be born.
“We’re always in the process of working on code,” Rosenberg says. “We kind of built the backbone and know when it’s about to change before it changes. For this project and others, we work hard to be at the forefront on code, and we guide cities on what we think is the right direction. We submitted a proposal to Culver City with ideas on zoning code and legal language.”
Boyd has received a grant from the National Science Foundation to work with ASTM to get structural engineering approval that meets building code for his Curve Appeal project, which aims for completion in Chattanooga in mid-summer 2018.
When Jorgensen completed the 3D printhuset, his team didn’t focus on changing local codes, because that would have been too time consuming. “Instead, we adjusted our construction to meet regulations. We have columns inside the house which carry the roof, wind load, etc.,” Jorgensen says.
What Does the Future Hold?
First, 3D printing could transform design by allowing new shapes and ideas to come to life. The logical progress is to incorporate more and more features, like insulation, plumbing, and electricity during the printing process, making it more turnkey and efficient.
“But no project in the world is near this maturity level yet, so we simply don't know how long it will take to reach it,” Jorgensen says.
Rosenberg and his team for the Print House want to gradually move to deploy the technology to build homes in third-world countries. “Our focus first is to fix Los Angeles in terms of being spread out and inefficient in construction,” he says. “We want to densify construction in one area.”
Their biggest challenge?
“Getting past legacy building technologies, which are slow and dated, and people are too used to them,” he says. “We have to complete the first one to show and quantify less use of manpower to change people’s perspective. That’s always the biggest challenge.”
Maura McCarthy, co-founder at Blu Homes and HIVE dean, will challenge her panel at HIVE to think about new ways to bring efficiencies to the construction process and breakthrough legacy practices. Register now to be part of the discussion.
This story appears as it was originally published on our sister site, www.hiveforhousing.com.
Jennifer Castenson
Jennifer Castenson serves as the director of thought leadership content for Hanley Wood. In this capacity, she provides leadership and collaboration across all verticals in the building products industry to drive innovation. Castenson establishes themes and coordinates content from Metrostudy, Hanley Wood’s industry leading data and research arm, along with content from the editorial team.
文章出处:《Function and Facts of 3D Printed Housing》